Page 1 of 1
2 stroke pipe repair
Posted: March 31st, 2009, 9:15 am
by DPinDet
I have a pipe from my CR250 that has a good size dent in it from a tree. I know I can send it off to various folks to get it repaired, but I am the kind of guys who likes to learn to do things myself. I have tried the water and freeze method with little results, if any. Has anybody tried to heat the area and use the compressed air method? If so, how much air pressure? Comments ?
DPinDet
Posted: March 31st, 2009, 9:44 am
by _joshua_
2 BAR max...
But stay very carreful!!!!
Re: 2 stroke pipe repair
Posted: March 31st, 2009, 10:52 am
by south central hoon
DPinDet wrote:I have a pipe from my CR250 that has a good size dent in it from a tree. I know I can send it off to various folks to get it repaired, but I am the kind of guys who likes to learn to do things myself. I have tried the water and freeze method with little results, if any. Has anybody tried to heat the area and use the compressed air method? If so, how much air pressure? Comments ?
DPinDet
I have a friend that is amazing using the compressed air method. not sure how much pressure, but i would start slow and build up pressure till she pops.
Posted: March 31st, 2009, 11:29 am
by _joshua_
Like this...
In french:
MODE OPERATOIRE
1 Mettre en place les deux brides
2 Mettre au rouge la surface concernée (chalumeau ou bec gaz)
3 Envoyer la pression (5 bars Maxi) et vous voyez la réparation se faire en 1 clin d'oeil , le métal reprend sa position initiale
Il faut aussi tapoter sur les bords avec un petit marteau là ou la tôle est la plus froissée ( au bord du cratère ); c'est à dire qu'il faut être 2 pour l'opération 1 qui gère le chalumeau et l'autre la pression et le marteau
Posted: March 31st, 2009, 12:36 pm
by hoofarted
Thats pretty much how Dewayne Jones does it as well. Not sure how much pressure though.
Posted: March 31st, 2009, 4:34 pm
by ISBB
1 bars = 14.5037738
The Frenchies say 5 bars which is a bit over 70 PSI someone else mentioned 2 bars which is 29ish psi.. so i say shoot for the middle and stick 45-50 in there and see what happens

Posted: March 31st, 2009, 5:00 pm
by asteroid500
my mate dose hundreds a year in Melboure, Australia.
100psi......NO im not kidding.
i was taut by him to do it and ive never blown one out.
if only i could wire weld as good as him.(oxy)
pipe repair
Posted: April 1st, 2009, 9:07 am
by DPinDet
Awesome! Thanks for the help guys.
DPinDet
Posted: April 1st, 2009, 11:17 am
by KE 336
I made plugs for both ends of pipe. Drilled and tapped the cyl. end plug to accept a male air fitting to connect the shop air hose to. I regulate the pressure @ 50-60psi. I think it is a good idea to "burn out" the pipe before plugging the ends and heating because it could become very explosive(the oily spooge inside) if you don't. Plug ends and apply pressure then use torch to start heating the dent. make circles around the dent starting on the outside and working towards the center. You have to get the metal good and red before the dent starts to slowly rise out.
Posted: April 1st, 2009, 1:17 pm
by Uzi
KE 336 wrote:. I think it is a good idea to "burn out" the pipe before plugging the ends and heating because it could become very explosive(the oily spooge inside) if you don't. Plug ends and apply pressure then use torch to start heating the dent. make circles around the dent starting on the outside and working towards the center. You have to get the metal good and red before the dent starts to slowly rise out.
Thats a must if you get a fire going in the pipe from the left over oil and carbon its not pretty! It can melt your plugs out and cause the pipe to blow out and be completely ruined not to mention the molten metal flying around!
Just get a dial regulator and put it in-line like you would on a paint gun so you can set the pressure accurately and safely.
Posted: April 6th, 2009, 6:38 pm
by KE 336
These are what I made up a few years ago to plug and supply air pressure.
This is before. It was a little more difficult to fix because of the funky bends it had on the welded seam.
After. Not perfect, but beats buying a new pipe everytime it gets dinged.
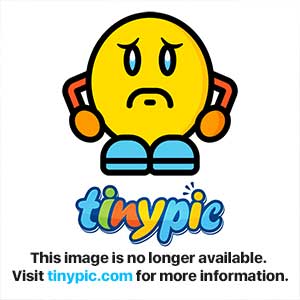