7/16 motor mount bolts
7/16 motor mount bolts
I've read before that drilling you cases and frame for larger 7/16" bolts helps reduce vibration. Is it really worth it. I'm getting ready to do another AF for myself and want to build a bike with the least vibes possible for a 500 smoker.
My brain is thinking that once you torque the 10mm honda bolts everything is sandwiched and the slop doesn't matter anymore. Can someone shed some light on the subject before I hog out a good set of cases?
My brain is thinking that once you torque the 10mm honda bolts everything is sandwiched and the slop doesn't matter anymore. Can someone shed some light on the subject before I hog out a good set of cases?
- maddog1927
- Posts: 313
- Joined: April 4th, 2010, 8:10 am
- Location: Mesa, AZ
The only person I have read that said anything about that was steve_k. He is doing a gen 3 conversion and has a build post near the top of the page on the other site.
I would not do it. I like the looks of a OEM flanged dimpled bolts. Mixing SAE components on a "metric" bike also bothers me. I do not see where it would reduce vibes either.
I would not do it. I like the looks of a OEM flanged dimpled bolts. Mixing SAE components on a "metric" bike also bothers me. I do not see where it would reduce vibes either.
- Roostius_Maximus
- Site Admin
- Posts: 4641
- Joined: November 16th, 2007, 3:24 pm
- Location: Mt Nebo, Manitoba, Canada
- Contact:
There are 3 different metric bolts tho. hourglass shaped ones, some with the shank just a bit smaller than the thread o.d. and some with the shank the same size as the thread o.d.
I don't know where the ones I used came from but the shank is the same size as the o.d. of the thread.
I don't know where the ones I used came from but the shank is the same size as the o.d. of the thread.
http://www.youtube.com/user/500bigbore
My CR500 Tech Reference... http://sdrv.ms/1a0CIiz
MRE Components... http://sdrv.ms/1bs2zhd

My CR500 Tech Reference... http://sdrv.ms/1a0CIiz
MRE Components... http://sdrv.ms/1bs2zhd

- 2strokeforever
- Posts: 1524
- Joined: November 13th, 2009, 1:04 pm
- Location: Vernon B.C Canada
- 2strokeforever
- Posts: 1524
- Joined: November 13th, 2009, 1:04 pm
- Location: Vernon B.C Canada
cmotodad wrote:Back in the old days we would not drill out the frames, we would find the right size bolt for the hole....
What he said ^^^ There are proper Honda bolts that were used - I just forget the part number. I think Danny may recall...
The CR500 is an acquired taste. If you don't like it, acquire some taste...
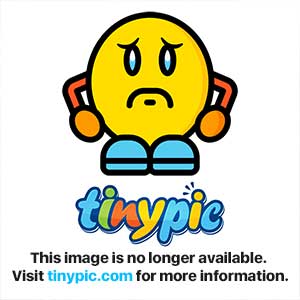
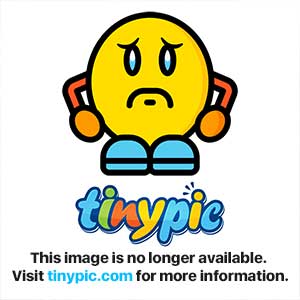
Bigger sized bolts are really only of use if you have a damaged frame mount - as in, it's flogged out from round. Assuming of course, the manufacturer / designer / builder has not made a very basic stuff up.
I'd prefer to machine the frame hole to true circular, then machine a 'top hat' insertable washer /spacer.
In a perfect world, we'd have inserts like those in the cases at the swingarm pivot, in all the engine mount points . And all the mount points perfectly aligned. But it would make for very expensive bikes.
Many of you blokes that have done your own AF conversions, or purchased one, will be aware of the 'migratory tendencies 'of a frame conversion, directly refering the the engine mounts, of course.
I've never had a flogged out frame. That indicates idiocy, on the part of someone. . A bit of a harsh judgement, I know.
A very important things in relation to stopping frame cracking, especially with an aluminium frame, is correct shimming / spacing of the engine to the frame (a known, significant problem with the KX500s), correct sized washers /bolt heads (and spacers /shims) against the frame - as in large enough diameter, without going too far, and Not putting the sharp side of a spacer / washer against the frame - or engine. And Not having a too large spacer / washer going onto a radius of a mount.
Of course, the engine mounts 'face' is and important factor - flat and true, is the only way for it to be.
Proper bolt torque / making sure mount bolts /nuts don't come loose, should be a given / obvious.
'Necked down' bolts are very much a feature of a very torque specific fitting - very prominent in engine main components, and many other high stress, size minimised applications. The slightly smaller shank as against thread bolts, you so often come across, is just a by product of loose standards, though it could be argued (and is) that it is a half way house to the trick / controlled 'necked down' bolts . In normal use, with normal, non outrageous torque needs, it's a non issue, especially with correct washer / shim / spacer useage
'True Sized', non 'Engineering Bolt', bolts can be difficult to come by. In my frame making business, I use them for applications in sheer. Shock mounts, linkage mounts , axle block / plates to swingarm mounts etc, so there is no movement between any parts, full diametric contact, no weak points. Many of my frames / swingarms etc, mount / pivot points dimensions, are influenced by the bolts that I can obtain. I've recently had to make subtle changes to my DH frames swingarm pivot width, because I can no longer get the exact 'bolt' that I have used for more than 15 years. Give something a chance to 'move' in sheer, and your on your way to failure. Having the shank of the bolt either part way into the mount that it threads into, or, in the case of a nut being used, having No thread bearing on the mounts, makes for an incredibly stronger fitment point. Full shank / correct dia., shank usage can mean you can go to a smaller bolt, whilst still being a much stronger fitment than a dodgy bolt that's bigger.
I mention all that, because it is very beneficial to Not have threaded sections bearing onto frame mounts, or the engine itself, both for sheer point reasons, and point contact stress risers. That's where outer washers / spacers (and inner spacers) are such an important thing. Aluminium frames really benefit from correct fitment / bolt / shim / spacer usage, but steel frames won't complain about being set up well.
With a steel swingarm I'm doing for a 500 project, I'm currently tearing my hair out as to whether I just do a full steel rear axle mount, a steel axle adaptor plate to the steel Swingarm, or an aluminium axle plate to the steel swingarm. It would make it easier for different wheel fitments, and a tad lighter, at the 'most traveled' point of the swingarm, but it will make for a fair bit of extra machining - but, it's how I've always done my DH swingarms. Decisions, decisions

I'd prefer to machine the frame hole to true circular, then machine a 'top hat' insertable washer /spacer.
In a perfect world, we'd have inserts like those in the cases at the swingarm pivot, in all the engine mount points . And all the mount points perfectly aligned. But it would make for very expensive bikes.
Many of you blokes that have done your own AF conversions, or purchased one, will be aware of the 'migratory tendencies 'of a frame conversion, directly refering the the engine mounts, of course.


I've never had a flogged out frame. That indicates idiocy, on the part of someone. . A bit of a harsh judgement, I know.
A very important things in relation to stopping frame cracking, especially with an aluminium frame, is correct shimming / spacing of the engine to the frame (a known, significant problem with the KX500s), correct sized washers /bolt heads (and spacers /shims) against the frame - as in large enough diameter, without going too far, and Not putting the sharp side of a spacer / washer against the frame - or engine. And Not having a too large spacer / washer going onto a radius of a mount.
Of course, the engine mounts 'face' is and important factor - flat and true, is the only way for it to be.
Proper bolt torque / making sure mount bolts /nuts don't come loose, should be a given / obvious.
'Necked down' bolts are very much a feature of a very torque specific fitting - very prominent in engine main components, and many other high stress, size minimised applications. The slightly smaller shank as against thread bolts, you so often come across, is just a by product of loose standards, though it could be argued (and is) that it is a half way house to the trick / controlled 'necked down' bolts . In normal use, with normal, non outrageous torque needs, it's a non issue, especially with correct washer / shim / spacer useage
'True Sized', non 'Engineering Bolt', bolts can be difficult to come by. In my frame making business, I use them for applications in sheer. Shock mounts, linkage mounts , axle block / plates to swingarm mounts etc, so there is no movement between any parts, full diametric contact, no weak points. Many of my frames / swingarms etc, mount / pivot points dimensions, are influenced by the bolts that I can obtain. I've recently had to make subtle changes to my DH frames swingarm pivot width, because I can no longer get the exact 'bolt' that I have used for more than 15 years. Give something a chance to 'move' in sheer, and your on your way to failure. Having the shank of the bolt either part way into the mount that it threads into, or, in the case of a nut being used, having No thread bearing on the mounts, makes for an incredibly stronger fitment point. Full shank / correct dia., shank usage can mean you can go to a smaller bolt, whilst still being a much stronger fitment than a dodgy bolt that's bigger.
I mention all that, because it is very beneficial to Not have threaded sections bearing onto frame mounts, or the engine itself, both for sheer point reasons, and point contact stress risers. That's where outer washers / spacers (and inner spacers) are such an important thing. Aluminium frames really benefit from correct fitment / bolt / shim / spacer usage, but steel frames won't complain about being set up well.
With a steel swingarm I'm doing for a 500 project, I'm currently tearing my hair out as to whether I just do a full steel rear axle mount, a steel axle adaptor plate to the steel Swingarm, or an aluminium axle plate to the steel swingarm. It would make it easier for different wheel fitments, and a tad lighter, at the 'most traveled' point of the swingarm, but it will make for a fair bit of extra machining - but, it's how I've always done my DH swingarms. Decisions, decisions


- asteroid500
- Posts: 1047
- Joined: January 5th, 2009, 1:29 am
- Location: Australia Melbourne
i was shown by some one when i was in my teens to always shim your motor into your frame to help reduce vibration & i do this with all my bikes, also in the case of the G-1 put the X brace back in... its got to work or Honda wouldnt of bothered doing it.
X welded in place G-1
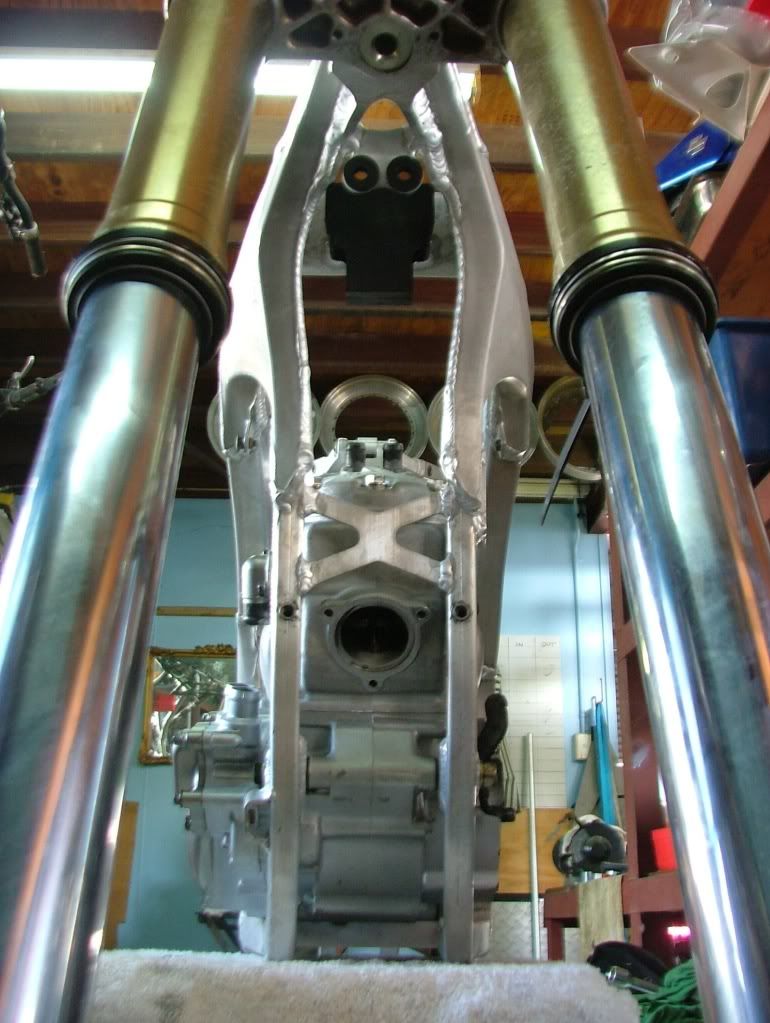
Shims can even be fitted by you ex wife ( be kind it still hurts-seriously)
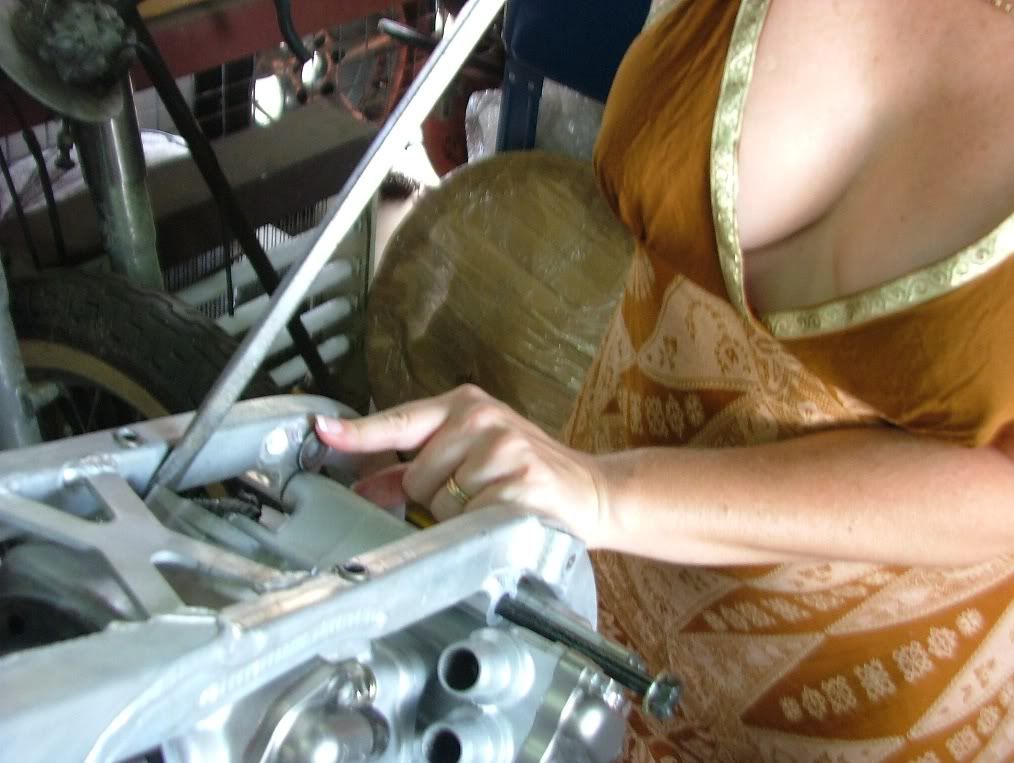
I also made replacement casing spacers taking out the movement in that area completely
.
X welded in place G-1
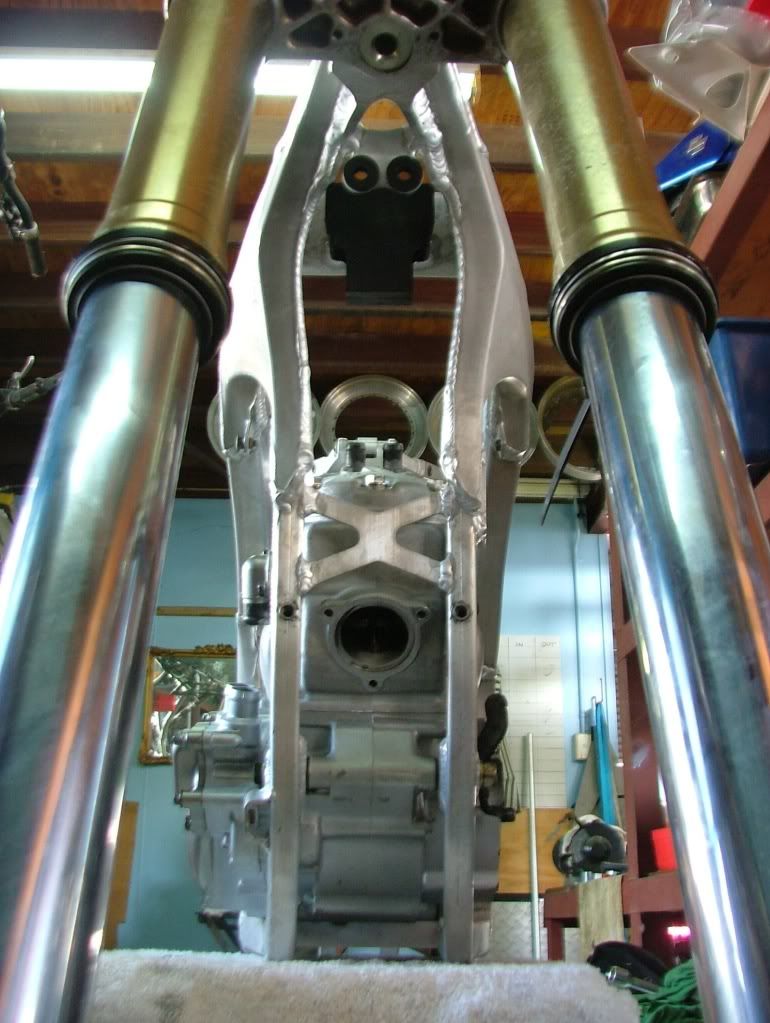
Shims can even be fitted by you ex wife ( be kind it still hurts-seriously)
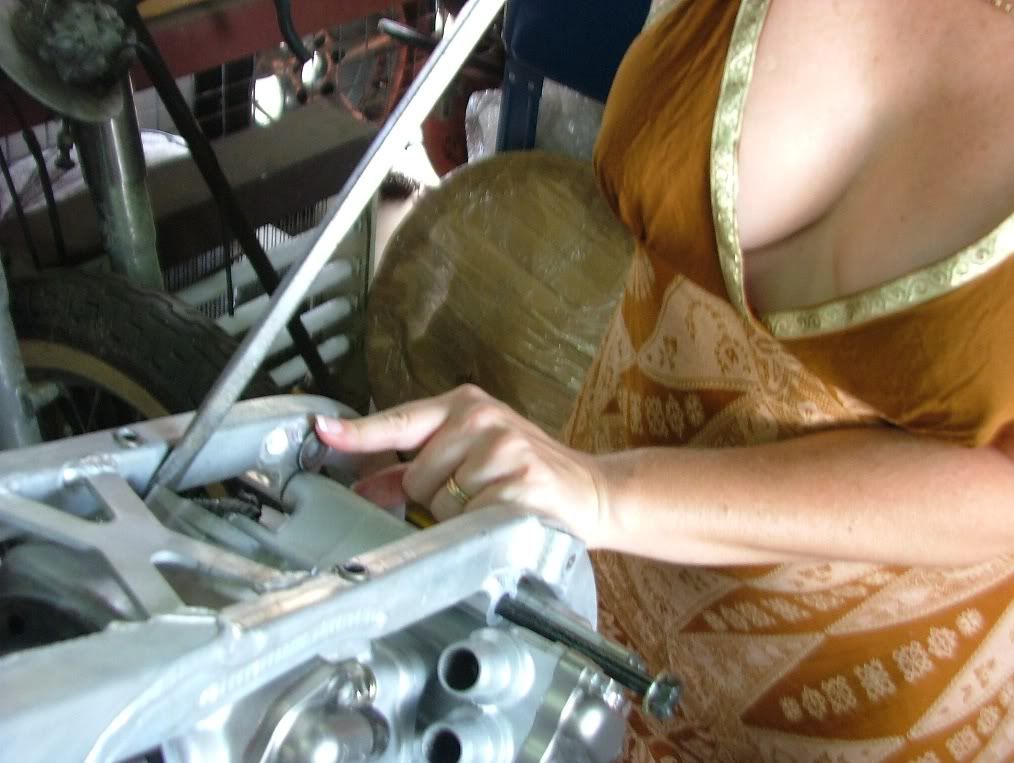
I also made replacement casing spacers taking out the movement in that area completely
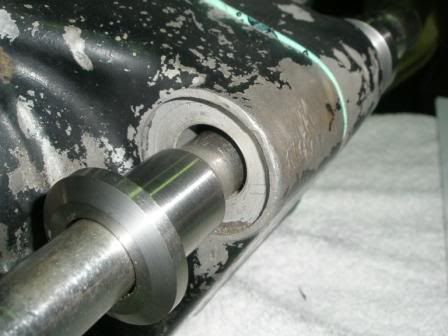
"not speeding officer".....qualifying
CR250 97
CR500 AF 99 (in progress)
CR500 AF CR G-4
CR500 1985 true legend
RGV250 96 X2
GSXR600 07 TRACK BIKE
VH Commadore cup car (race)
CR250 97
CR500 AF 99 (in progress)
CR500 AF CR G-4
CR500 1985 true legend
RGV250 96 X2
GSXR600 07 TRACK BIKE
VH Commadore cup car (race)
I shimed everything, made a two sided headstay, and match drilled every hole to 7/16" after the bike was 100% assembled.asteroid500 wrote:i
My A/F vibes less that any other I have rode, others have made the same comment....
7/16" is 11mm. I wouldnt call opening up the hole .5mm on each side "Hogging it out". The holes in the cases are damm near 11mm already.
Draw your own conclusions....
- Gravel Scratcher
- Posts: 278
- Joined: September 20th, 2009, 8:45 pm
- Location: Australia, Central QLD
Thus my line of questioning. I remember you sayin you did it and it didn't vibe much. I just don't get why the bolts make a difference.AlisoBob wrote:
I shimed everything, made a two sided headstay, and match drilled every hole to 7/16" after the bike was 100% assembled.
My A/F vibes less that any other I have rode, others have made the same comment....
7/16" is 11mm. I wouldnt call opening up the hole .5mm on each side "Hogging it out". The holes in the cases are damm near 11mm already.
Draw your own conclusions....
To have the lowest vibes.... you want the bike assembled as one gigantic mass. The bigger the mass, the harder it is to buzz.
The frame, engine, and exhaust need to be monolithic., not 3 seperate pieces hung together willy-nilly.
Also, you dont want the frame pinched together, or spread apart.
So, the best way to get there?
Releive any tight spots between the frame and the motor, or shim any gaps closed. The motor should FIT, not be crammed in there.
Then, hang the exhaust with all the OEM hangers, with all the rubbers and spacers present and in good shape.
I also only reccomend a two sided headstay.
And lastly, I match drill all the mounting bolts to 7/16" (11mm) to make sure everything fits perfectly. Welding sometimes moves things around a little.
There was one photo posted where some guy pulled his motor out after riding the bike for awhile... and you could see movement marks at every motor mount / tab connection.
He complained the bike vibed badly too.....
2+2=4
The frame, engine, and exhaust need to be monolithic., not 3 seperate pieces hung together willy-nilly.
Also, you dont want the frame pinched together, or spread apart.
So, the best way to get there?
Releive any tight spots between the frame and the motor, or shim any gaps closed. The motor should FIT, not be crammed in there.
Then, hang the exhaust with all the OEM hangers, with all the rubbers and spacers present and in good shape.
I also only reccomend a two sided headstay.
And lastly, I match drill all the mounting bolts to 7/16" (11mm) to make sure everything fits perfectly. Welding sometimes moves things around a little.
There was one photo posted where some guy pulled his motor out after riding the bike for awhile... and you could see movement marks at every motor mount / tab connection.
He complained the bike vibed badly too.....
2+2=4
So if I'm understanding this correctly regarding the size of the bolts being bigger is the motor shakes less in the mounts?
I was under the impression that when the motor fits the mounts correctly, tightening the bolts would create the monolithic mass. I could easily see if it was shaking in the mounts how the larger bolt would help.
I was under the impression that when the motor fits the mounts correctly, tightening the bolts would create the monolithic mass. I could easily see if it was shaking in the mounts how the larger bolt would help.
I used all OEM bolts and nuts, and tightened and loctite and have been happy, if I were showing any issue of vibe/loosening I would match drill/etc, although trying to find quality hardware that is properly sized is a helluva time.
I played with Honda part#s until I found OEM motor mount bolts in proper sizes.. Think they were from a trx quad or something.
I played with Honda part#s until I found OEM motor mount bolts in proper sizes.. Think they were from a trx quad or something.
OK. I knew what you meant about the match fit being the issue not the size. 7/16 is just the next smallest easily attainable size to do.
So on your build Bob did you do jut the lower and front motor mounts, the ones with the long bolts? Or did you do this with the head stay bolts as well?
Maybe with some luck I can find bolts for the motor mounts that have the full dimension thru the mounts on the frame and the threads starting on the outside of that.
Will a die work on grade 8 bolts? Is grade 8 overkill?
So on your build Bob did you do jut the lower and front motor mounts, the ones with the long bolts? Or did you do this with the head stay bolts as well?
Maybe with some luck I can find bolts for the motor mounts that have the full dimension thru the mounts on the frame and the threads starting on the outside of that.
Will a die work on grade 8 bolts? Is grade 8 overkill?
I only did the main bolts, the OEM headstay bolts are close tolerance, and fit well.seanmx57 wrote:So on your build Bob did you do jut the lower and front motor mounts, the ones with the long bolts? Or did you do this with the head stay bolts as well?
Will a die work on grade 8 bolts? Is grade 8 overkill?
A sharp die will cut a grade 8 bolt.